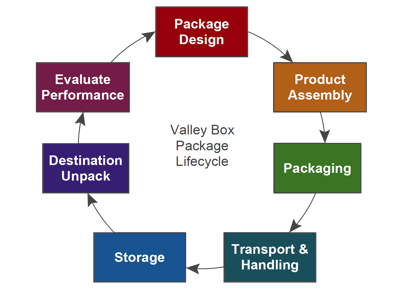
Valley Box Company, a San Diego crating manufacturer, welcomes you to this 7-part series exploring the package lifecycle with a focus on matching you with the right packaging method for your product.
You have a few options moving forward.
- Voracious Reader: Below you'll find a blog-transcript of this first section in the Package Lifecycle.
- Press Play: If you want to sit back, relax and let us do the talking watch the video of the presentation below!
The first step of the lifecycle is the Package Design Phase. The best time to consider package design can depend on your type of manufacturing process and your product. Design challenges can be overcome by involving your San Diego crating vendor during the early product development phase.
For the purposes of this series, we’ll break down manufacturers into three types.
Types of Manufacturers
A “type 1” manufacturer includes products that are produced in daily larger quantities rolling off an assembly line - like bottling or semiconductors. The time to address your packaging should be prior to any manufacturing. Treat the packaging as part of the product rather than an afterthought. If your product is moved, handled, or staged during production, it may be cost effective to incorporate the packaging into your process as a function of material handling.
A “type 2” manufacturer may make a product that is larger dimensionally, and the throughput time can range from a week to months - like machinery or computerized manufacturing equipment. The product’s design may be the same or vary to customer requirements, but would generally ship assembled with few ancillary packages. The time to address your packaging should be during the product production phase, in order to avoid shipping delays.
A “type 3” manufacturer is similar to a type two but may be make product that is more customized - like custom conveyor systems or whole production lines. Packaging designs are usually addressed once the product is completed as the product may undergo last minute modifications and possible dis-assembly due to various shipping challenges.
Type 3 Manufacturer Case Study
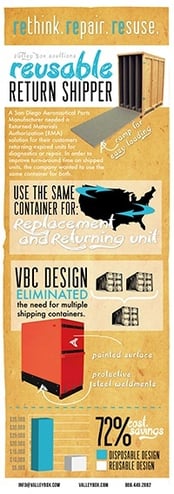
An Aircraft Company manufactures large and heavy milled rings, which require off-site machining by a sub-contractor, who then ships the rings back to the point of origin.
Valley Box suggested a reusable wooden shipping crate rather than a one-way shipper. The reusable features provided long-term durability and included:
- Steel
- Hardware
- Waterproofing
- An attached loading ramp.
Assuming a performance lifespan of at least 5 years, the savings of this reusable wooden shipping crate design out weighed the cost of replacing each one-way shipper. Other benefits included:
- Expedited round-robin shipments
- Reduced packaging waste associated with one-way shippers
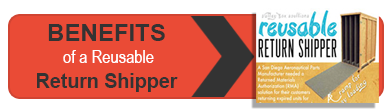
Type 1 Manufacturer Case Study
Why does it matter to have a plan prior to shipment? Well if you are utilizing international sea containers or freight trucking, designing packaging to optimize the payload can dramatically reduce the cost.
By implementing a packaging plan in advance, you can load a higher value of goods while the freight charges remain constant. When voids of space occur within the load, blocking and bracing is necessary to avoid load shifting that can potentially destroy the contents. By creating a packaging configuration that best utilizes the internal dimensions of the containers, labor & materials for such blocking and bracing are greatly reduced.
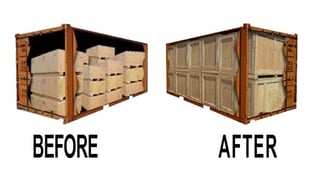
Challenge: Here is another case study for a Parts Machining Manufacturer who needed to optimize the outside dimensions of their wood boxes, in order to efficiently pack their overseas shipping container.
Solution: Valley Box designed heat treated wooden shipping crates that held the maximum amount of parts while not exceeding the maximum dimensions. Additionally this method saved time during loading and unloading by eliminating blocking and bracing needs.
Packaging Materials
There are many types of packaging materials to choose from, it’s important to understand the differences of each material.
- Corrugated boxes: Single wall and double wall boxes are good for a Type 1 company who have a higher rate of usage and buy in large repetitive quantities.
- Triple Wall: A triple fluted corrugated box. This material is a light weight tough, rugged material that works well for air freight or when the cost of freight is weight sensitive. Since it is fiber board, triple wall may not be desirable for long term outdoor storage. A similar sized standard wood container could weigh nearly 40% more impacting your freight costs.
- Wooden Shipping Crates: Wood crates can potentially offer a more economic outer package than its paneled wood box counterpart. It can be a cost effective choice when determining the level of protection your product really needs.
- Light & Heavy Duty Wooden Crates: These beefy crates are perfect for the Type 2 & 3 Manufacturer. They are durable and customizable to your product. These styles of boxes can be built to hold payloads of any size and weight.
Package Closure & Opening Safety
When discussing the package design with your San Diego crating vendor, addressing the method of closure and end customer opening is vital. How you close the package determines how it will be opened.
This can impact the end user in that tools and manpower may be needed. If an end user sustains an injury attempting to open your package, this not only becomes a potential liability to you, but could alter the perception of Your Products Quality.
There are many ways to secure a package. Some methods like strapping require specific tools. All tapes can be applied easily, and stretch wrap is quick at securing palleted stacks of products.
Discuss what is most cost effective with appropriate performance levels with your San Diego crating supplier.
Watch more of the series
- Packaging Design - Watch the Video - Read the Blog - View the Slideshow
- Product Assembly - Watch the Video - Read the Blog - View the Slideshow
- Packaging Process - Watch the Video- Read the Blog - View the Slideshow
- Transport and Handling - Watch the Video - Read the Blog - View the Slideshow
- Storage - Watch the Video - Read the Blog - View the Slideshow
- Destination Unpack - Watch the Video - Read the Blog - View the Slideshow
- Evaluation of Performance - Watch the Video - Read the Blog - View the Slideshow